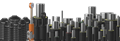
Introduction to KALLER products
An introductory overview of KALLER products to learn more of the broad variety, the different benefits and features, and various solutions we offer.
Contents:
- Why Choose Gas Springs?
- Why Choose KALLER?
- What Kind of Products does KALLER Provide?
- Standard Gas Springs
- Problem Solvers & Cost-Reduction Solutions
- Safety & Reliability - Reduce Your Risks
- Remote Pressure Monitoring Systems
- Mounts, Accessories, & More
- Gas Spring Selection Guide
Did you also know that when you choose KALLER you also get our various Support and Services?
Why Choose Gas Springs?
Compared to coil springs or hydraulics, nitrogen gas springs provide impressive force in a compact space. They do not leak contaminating hyraulic or other fluids that can damage produced parts or the surrounding workspace.
Compared to Coil Springs
|
Compared to Hydraulics
|
Why Choose KALLER?
- Trusted Worldwide: KALLER products are consistently trusted by major OEMs because they are designed and manufactured to have the best Quality, Safety, and Reliability in the market.
- Save with KALLER: With reliable quality and cost-reduction solutions you can ensure a smooth operation with less downtime, less scrap parts, and better part quality.
- Service & Support: For over 40 years we have provided unparrallel support for application solutions, practical and online training, calculators & tools, and a variety of other services to ensure you are provided the help you need.
- Available Globally & Locally: Through our vast global network that both supplies and provides support, you kind find KALLER around the world from your local service point or distributor.
- The Leader in Safety: Reduce risks and liabilities with KALLER's advanced Safety Features and design.
What Kind of Products does KALLER Provide?
Standard Gas Springs
![]() |
With a very large selection, many of our standard springs are found on major OEM and company standards around the world because of the top-tier Quality, Safety, and Reliability. KALLER Gas springs are designed, manufactured, and tested for top quality and are approved according to PED 2014/68/EU. |
See our Gas Spring Selection Guide below.
Calculate According to Your Operation
Find the right configuration with our Calculators and Configure according to various parameters.
![]() |
![]() |
![]() |
Force & Temperature Calculator Determine the force profile and operating temperature for Gas Springs. |
Simplifies the selection process for flex cam systems. |
Controllable Gas Springs KF Calculator Determine system and cooling performance for Controllable Gas Springs (KF). |
Problem Solvers & Cost-Reduction Solutions
We offer a variety of solutions to fit your needs, see a list of a few below. Also, see our Cost Effective Guide for detailed guides on cost saving solutions.
Product/ Series | Benefits | |
![]() |
KF2 (Controllable Gas Springs/ Delayed Return Unit) | Reduce the number of dies, improve part quality, & reduce downtimes. See the Case Study |
![]() |
Flex Cams | Reduce tooling costs, reduce maintenance, & able to be retrofitted. See the Case Study |
![]() |
LCF Series (Low Contact Force) | Reduce shock load, reduce pad/ blank-holder bounce, noise reduction. |
![]() |
SPC Series (Speed Control) | Reduce blank holder bounce, increase strokes per minute, & increase productivity. See the Case Study |
![]() |
HDP (Protective Covers) | Reduce maintenance times, prolong gas spring lifetime, & reduce downtimes. See Hot Stamping Example |
![]() |
Toolmind (Remote Pressure Monitoring) | Monitor and stop production when pressure or temperature is outside set perameters. |
Safety & Reliability - Reduce Your Risks
Reduce unnecessary safety risks and liabilities with KALLER quality as well as incorporated feature designs to keep you safe and production running reliabily.
Safety Features:
![]() |
![]() |
![]() |
Prevents the gas spring bursting in the event of an over stroke. |
Prevents the piston rod on the gas spring from ejecting. |
Prevents the gas spring bursting in the event of an over pressure. |
Reliability Features:
Remote Pressure Monitoring System - Toolmind
Toolmind is a remote monitoring system that seamlessly integrates into new and existing production systems.
![]() |
Benefits:
|
Mounts, Accessories, & More
Mounts
Accessories
KALLER Accessories are to make your life easier with installation, adjustment, use, and maintenance of KALLER gas springs.
![]() |
Gas Link Systems: A variety of Control Blocks and Hoses. |
Equipment and Tools: To assist during servicing and filling/ charging of nitrogen gas springs.
|
|
![]() |
HDP (Heavy Duty Protection): Protective covers in contaminating environments to ensure smoother and more reliable production times with less maintenance. |
More
![]() |
Manifold Systems: The SuperBrute® Nitrogen Manifold Systems by Forward provides seamless die transitions, constant force, adjustable pressure and simplified maintenance. |
![]() |
Basplate Systems: As part of General Motors (GM) standard requirements, Base Plate systems are an alternative Gas Link systems without external or exposed hoses |
Need Help Choosing? Right for the Application? | Contact Us!
With decades of experience in finding solutions to various applications, backed by a global network of experts, we are glad to assist you in finding the right gas spring for your needs.
Contact us directly or find your nearest distributor on the Contact Us page.
Gas Spring Selection Guide
Series |
Description |
Gas Spring Model |
Stroke Lengths |
Initial Force at Max. Pressure |
Total Length |
Cylinder Diameter |
|
(mm) | (N) | (lbf) | (mm) | (mm) | |||
EP3 16 |
Color coded gas Ejector-Pins, interchangeable with mechanical spring plungers. | EP3 16 | 10-125 | 420 | 95 | 45+(2xStroke) | M16x1.5/M16x2 |
EPS3 16 |
EPS3 16 | 10-125 | 420 | 95 | 45+(2xStroke) | M16x1.5 | |
EP2 24 |
EP2 24 | 10-125 | 1,700 | 382 | 45+(2xStroke) | M24x1.5 | |
EPS2 24 |
EPS2 24 | 10-125 | 1,700 | 382 | 45+(2xStroke) | M24x1.5 | |
R12 |
Rod sealed and color coded gas springs – compact and fully adjustable. | R12 | 7-125 | 500 | 112 | 56-295 | Ø12 |
R15 |
R15 | 7-125 | 700 | 160 | 56-295 | Ø15 | |
R19 |
R19 | 7-125 | 900 | 202 | 56-295 | Ø19 | |
M2 |
Repairable, color coded and fully adjustable gas springs available with or without threaded cylinders. | M2 | 10-125 | 2,000 | 450 | 62-295 | Ø25 |
MM2 |
MM2 | 10-125 | 2,000 | 450 | 42+(2xStroke) | M28x1.5 | |
MC3 |
MC3 | 10-125 | 2,000 | 450 | 50+(2xStroke) | Ø32 | |
MC3-SP |
MC3-SP | 10-125 | 2,000 | 450 | 50+(2xStroke) | Ø32 | |
CU4 |
Super compact gas springs providing extreme initial forces with minimal cylinder diameters. | CU4 420 | 6-50 | 4,250 | 955 | 56-195 | Ø25 |
CU4 740 | 6-50 | 7,400 | 1,660 | 63-195 | Ø32 | ||
CU4 1000 | 6-50 | 10,600 | 2,400 | 61-230 | Ø38 | ||
CU4 1800 | 6-65 | 18,000 | 4,050 | 66-271 | Ø50 | ||
CU4 2900 | 10-65 | 29,500 | 6,630 | 85-256 | Ø63 | ||
CU4 4700 | 10-65 | 47,000 | 10,570 | 80-273 | Ø75 | ||
CU4 7500 | 10-65 | 75,000 | 16,860 | 90-279 | Ø95 | ||
CU4 11800 | 10-65 | 118,000 | 26,530 | 100-320 | Ø120 | ||
CU4 18300 | 10-65 | 183,000 | 41,140 | 110-323 | Ø150 | ||
CX |
Compact Xtreme CX gas springs provide extreme forces by enabling high charge pressures. | CX 500 | 10-80 | 5,100 | 1,150 | 75-145 | Ø32 |
CX 1000 | 10-80 | 9,800 | 2,200 | 75-240 | Ø38 | ||
CX 1900 | 10-80 | 19,200 | 4,320 | 80-245 | Ø50 | ||
X |
As the Power Line Flagship, the X Series is the world’s shortest, strongest and most advanced rod sealed gas springs. | X 170 | 7-125 | 1,700 | 382 | 44-285 | Ø19 |
X 320 | 7-125 | 3,200 | 720 | 44-285 | Ø25 | ||
X 350 | 10-125 | 3,600 | 810 | 30+(2xStroke) | Ø32 | ||
X 500 | 10-125 | 4,700 | 1,055 | 30+(2xStroke) | Ø38 | ||
X 750 | 10-125 | 7,400 | 1,665 | 32+(2xStroke) | Ø45 | ||
X 1000 | 13-125 | 9,200 | 2,068 | 38+(2xStroke) | Ø50 | ||
X 1500 | 13-125 | 15,000 | 3,375 | 44+(2xStroke) | Ø63 | ||
X 2400 | 16-125 | 24,000 | 5,396 | 45+(2xStroke) | Ø75 | ||
X 4200 | 16-125 | 42,000 | 9,440 | 58+(2xStroke) | Ø95 | ||
X 6600 | 16-125 | 66,300 | 14,905 | 68+(2xStroke) | Ø120 | ||
X 9500 | 19-125 | 95,000 | 21,400 | 78+(2xStroke) | Ø150 | ||
X 20000 | 19-125 | 200,000 | 45,000 | 110+(2xStroke) | Ø195 | ||
XG |
The Power Line XG series is based on the X series with the same features but additional total length providing a larger G 1/8" charge port and longer bottom threads. | XG 350 | 10-125 | 3,600 | 810 | 40+(2xStroke) | Ø32 |
XG 500 | 10-125 | 4,700 | 1,055 | 40+(2xStroke) | Ø38 | ||
XG 750 | 10-125 | 7,400 | 1,665 | 47+(2xStroke) | Ø45 | ||
XG 1000 | 13-125 | 9,200 | 2,068 | 52+(2xStroke) | Ø50 | ||
XG 1500 | 13-125 | 15,000 | 3,375 | 52+(2xStroke) | Ø63 | ||
XG 2400 | 16-125 | 24,000 | 5,396 | 59+(2xStroke) | Ø75 | ||
XG 4200 | 16-125 | 42,000 | 9,440 | 62+(2xStroke) | Ø95 | ||
XG 6600 | 16-125 | 66,300 | 14,905 | 72+(2xStroke) | Ø120 | ||
XF |
The Power Line XF series is based on the X series with the same features but additional 10 mm total length providing a larger G 1/8” charge port. | XF 750 | 10-125 | 7,400 | 1,665 | 42+(2xStroke) | Ø45 |
XF 1000 | 13-125 | 9,200 | 2,068 | 48+(2xStroke) | Ø50 | ||
XF 1500 | 13-125 | 15,000 | 3,375 | 54+(2xStroke) | Ø63 | ||
XF 2400 | 16-125 | 24,000 | 5,396 | 55+(2xStroke) | Ø75 | ||
TX |
The Power Line Heavy Duty series, a crossover between the standard TU series and the Power Line X series. Total length same as TU, force same as X. | TX 750 | 13-200 | 7,400 | 1,665 | 85+(2xStroke) | Ø45 |
TX 1000 | 13-300 | 9,200 | 2,068 | 95+(2xStroke) | Ø50 | ||
TX 1500 | 13-300 | 15,000 | 3,375 | 95+(2xStroke) | Ø63 | ||
TX 2400 | 25-300 | 24,000 | 5,396 | 110+(2xStroke) | Ø75 | ||
TX 4200 | 25-300 | 42,000 | 9,440 | 120+(2xStroke) | Ø95 | ||
TX 6600 | 25-300 | 66,300 | 14,905 | 140+(2xStroke) | Ø120 | ||
TX 9500 | 25-300 | 95,000 | 21,400 | 155+(2xStroke) | Ø150 | ||
TX 20000 | 25-300 | 200,000 | 45,000 | 160+(2xStroke) | Ø195 | ||
TL |
The TL gas spring is shorter than the corresponding TU by 25 mm, except TL 5000 and TL 7500, which are 37.5 and 50 mm shorter respectively. | TL 750 | 12.5-250 | 7,400 | 1,665 | 70+(2xStroke) | Ø50 |
TL 1500 | 12.5-250 | 15,000 | 3,375 | 85+(2xStroke) | Ø75 | ||
TL 3000 | 12.5-250 | 30,000 | 6,750 | 95+(2xStroke) | Ø95 | ||
TL 5000 | 25-250 | 50,000 | 11,240 | 102.5+(2xStroke) | Ø120 | ||
TL 7500 | 25-250 | 75,000 | 16,860 | 105+(2xStroke) | Ø150 | ||
TU |
The TU gas springs' dimensions are the basis of the ISO 11901 standard for gas springs as well as the Ford WDX and GM gas spring standards. | TU 250 | 10-125 | 2,650 | 600 | 50+(2xStroke) | Ø38 |
TU 500 | 10-160 | 4,700 | 1,055 | 85+(2xStroke) | Ø45 | ||
TU 750 | 12.7-300 | 7,400 | 1,665 | 95+(2xStroke) | Ø50 | ||
TU 1500 | 25-300 | 15,000 | 3,375 | 110+(2xStroke) | Ø75 | ||
TU 3000 | 25-300 | 30,000 | 6,750 | 120+(2xStroke) | Ø95 | ||
TU 5000 | 25-300 | 50,000 | 11,240 | 140+(2xStroke) | Ø120 | ||
TU 7500 | 25-300 | 75,000 | 16,860 | 155+(2xStroke) | Ø150 | ||
TU 10000 | 25-300 | 106,000 | 23,830 | 160+(2xStroke) | Ø195 | ||
TUS |
The High Speed gas springs (TUS) have been engineered to withstand press stroke speeds to a maximum of 2 m/s. | TUS 750 | 25-300 | 7,4000 | 1,665 | 95+(2xStroke) | Ø50 |
TUS 1500 | 25-300 | 15,000 | 3,375 | 110+(2xStroke) | Ø75 | ||
TUS 3000 | 25-300 | 30,000 | 6,750 | 120+(2xStroke) | Ø95 | ||
TUS 5000 | 25-300 | 50,000 | 11,240 | 140+(2xStroke) | Ø120 | ||
TUS 7500 | 25-300 | 75,000 | 16,860 | 155+(2xStroke) | Ø150 | ||
LCF |
These innovative Low Contact Force gas spring are 100% interchangeable with ISO gas springs (i.e. TU series) and reduce shock loads, noise levels and pad bounce problems. | LCF 750 | 12.7-300 | 7,400 | 1,665 | 95+(2xStroke) | Ø50 |
LCF 1500 | 25-300 | 15,000 | 3,375 | 110+(2xStroke) | Ø75 | ||
LCF 3000 | 25-300 | 30,000 | 6,750 | 120+(2xStroke) | Ø95 | ||
LCF 5000 | 25-300 | 50,000 | 11,240 | 140+(2xStroke) | Ø120 | ||
LCF 7500 | 25-300 | 75,000 | 16,860 | 155+(2xStroke) | Ø150 | ||
LCF 10000 | 25-200 | 106,000 | 23,830 | 160+(2xStroke) | Ø195 | ||
SPC |
Speed Control™ reduce or eliminate blank holder bounce; commonly associated with increased return stroke speeds from new generation of presses. | SPC 750 | 80-300 | 7,400 | 1,665 | 110+(2xStroke) | Ø75 |
SPC 1500 | 125-300 | 15,000 | 3,375 | 120+(2xStroke) | Ø95 | ||
SPC 3000 | 125-300 | 30,000 | 6,750 | 140+(2xStroke) | Ø120 | ||
SPC 5000 | 125-300 | 50,000 | 11,240 | 155+(2xStroke) | Ø150 | ||
MT |
Mould Temp gas springs are compact and powerful piston rod sealed gas springs, which can be used up to 120°C. | MT 16 | 10-80 | 420 | 95 | 48+(2xStroke) | M16x1.5 |
MT 24 | 10-80 | 1,700 | 382 | 48+(2xStroke) | M24x1.5 | ||
MT 300 | 10-80 | 3,000 | 675 | 30+(2xStroke) | Ø32 | ||
MT 500 | 10-80 | 4,700 | 1,055 | 30+(2xStroke) | Ø38 | ||
MT 750 | 10-80 | 7,440 | 1,665 | 32+(2xStroke) | Ø45 | ||
MT 1000 | 13-80 | 9,200 | 2,068 | 38+(2xStroke) | Ø50 |