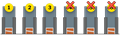
Introduction to Solutions & Cost Reducers
There are many challenges in die tool designing and stamping- and KALLER produces several solutions to common problems to optimize your operation.
Find the Solution to Your Challenge
Challenge | Solution |
---|---|
Reduce Scraps | Flex Cam | KF2 | Toolmind |
Reduce Tooling Costs | Flex Cam | KF2 | HDP |
Add Multi-functionality to a Tool | Flex Cam | KF2 |
Increase Production/ Operation Speed & Efficiency | Flex Cam | KF2 | SPC | HDP | Toolmind |
Reduce Downtimes, Damages & Maintenance | Flex Cam | KF2 | HDP | Toolmind |
Improve Part Quality | KF2 | Toolmind |
Reduce/ Controlled Return Stroke | KF2 | SPC |
Reduce Shock Load & Pad or Blank Holder Bounce | LCF | SPC |
Noise Reduction | LCF |
Flex Cam
The KALLER Flex Cam is state-of-the-art in hindering several common industry challenges.
Key Benefits:
- Reduce scraps
- Reducing tooling costs
- Simplifying die design
- Punches at upwards at negative angles
- Adds operation or multi-functionality to a die
- Protects against tool damage and over-pressure
- Improve production efficiency
See our Case Study Example of the Flex Cam.
New to Flex Cam?
Get an introduction to the Flex Cam on the KALLER Academy Courses:
- Flex Cam - The Application
- Flex Cam - Function, System, and Configuration
- Flex Cam - Filling and Bleeding
KF2 - Controllable Gas Springs
Since our invention in 1995, the KF2 has been exceptionally popular among tool designers due to its precision performance and cost saving capabilities.
Key Benefits:
- Reduce number of dies in an operation by adding multi-functionality to a die
- Reduce downtimes
- Improve part quality & reduce scraps
- Enhanced precision stamping
- Controlled return stroke for delicate materials
- Higher production efficiency & speed
- Cost-effective manufacturing
See our Case Study Example of the KF2 in action and Blog Post of increasing speed.
New to KF2?
Get an introduction to KF2 in our KALLER Academy courses:
LCF Series - Low Contact Force
The LCF Series is designed to provide a solution to several common industry challenges.
Key Benefits:
- Shock Load Reduction: Minimize press maintenance with reduced shock load and less wear on drive components.
- Pad/ Blank-holder Bounce Reduction: Improve part transfer efficiency, increase production rates, and reduce scrap by reducing the pad/ blank-holder bounce.
- Noise Reduction: Improve workspace noise levels, increase safety, and limit the necessity to incorporate noise enclosers with lower noise levels from the LCF Series compared to standard gas springs.
Features:
- 100% interchangeable with standard height (ISO) gas springs
- Drop-in, flange mount, or base plate mounting
- Charged and rebuilt like standard gas springs
- Can be linked together in a hose system
SPC Series - Speed Control
By reducing the speed of the return stroke, the SPC Series Gas Springs reduces blank holder bounce.
Key Benefits:
- Minimizes or eliminates blank holder bounce
- Minimizes damage to the pressing tool and die
- Increases productivity by increasing part transfer efficiency
- Increases strokes per minute in most implementations
- Can be retrofitted to existing dies
- Is linkable by using a hose system
- Is available in stroke lengths 80 to 300 mm
See our Case Study of the SPC Gas Spring Series.
HDP - Heavy Duty Protection
As an added accessory, the HDP covers provide additional protection to gas springs in dirty or contaminating environments. With this extra protection you can improve your operation efficiency and reduce unnecessary costs.
Key Benefits:
- Reduce downtime
- Reduce maintenance frequencies
- Reduce damages
- Reduce need for replacements
- Prolongs gas spring lifetime
- Maximizes production throughput and reliability
- Easy integration
Use Cases & Protection:
- Hot Stamping
- Galvanized materials
- Oil and grease
- Dust and dirt
- Wax and slivers
Toolmind - Remote Pressure Monitoring
Toolmind™ Remote Pressure Monitoring System is an easy-to-use monitoring system with triggers to automatically notify and stop the production of faulty parts when either pressure or temperature is outside the designated range.
Key Benefits:
- Quickly and easily view system status and data of pressure and temperature
- Faster change out times from storage to production
- Reduce scrap and damages by automatically stopping production with set triggers
- Proactive and efficient maintenance
- No subscriptions or monthly fees
- All data stays local in a fully connected ecosystem
Ask an Expert
Want to learn more about how KALLER can improve your operation? Contact Us today and speak to one of our experts to optimize your operation.